Courtesy: zed certification
he performance standard is Zero Defects”
Workers, at least during the post–World War II economic expansion, had a lackadaisical attitude on the whole toward work. Crosby saw statistical quality control and the MIL-Q-9858 standard as contributing to this through acceptable quality levels—a concept that allows a certain number of acceptable defects and reinforces the attitude that mistakes are inevitable. 80 79–80 Another contributor is the self-imposed pressure to produce something to sell, even if that thing is defective. 72–73 Workers must “make the attitude of Zero Defects [their] personal standard.”
“The measurement of quality is the price of nonconformance”
To convince executives to take action to resolve issues of poor quality, costs associated with poor quality must be measured in monetary terms.: 121 Crosby uses the term “the price of nonconformance” in preference to “the cost of quality” to overcome the misimpression that higher quality requires higher costs. The point of writing Quality Is Free was to demonstrate that quality improvement efforts pay for themselves. Crosby divides quality-related costs into the price of conformance and the price of nonconformance. The price of conformance includes quality-related planning, inspection, and auditing; the price of nonconformance includes scrap, rework, claims against warranty, unplanned service.
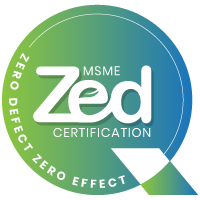
The main criticism is the amount of effort required to verify every person’s performance in an organization Confidence in the program, and therefore compliance with it, fades without this verification.
Point 10 of Deming’s 14 points (“Eliminate slogans, exhortations, and targets for the work force asking for zero defects and new levels of productivity.“) is clearly aimed at ZD. Joseph M. Juran was also critical of ZD.
Another criticism is that Zero Defects is a motivational program aimed at encouraging employees to do better. Crosby stated that “Motivation has nothing to do with it…It is merely setting performance standards that no one can misunderstand and then starting a two-way communications exercise to let everyone know about it.” He blamed management actions and attitudes for creating the opportunity for defects