Courtesy: Six sigma green belt
Methodologies
Six Sigma projects follow two project methodologies, inspired by W. Edwards Deming’s Plan–Do–Study–Act Cycle, each with five phases.
- DMAIC (“duh-may-ick”, /də.ˈmeɪ.ɪk/) is used for projects aimed at improving an existing business process
- DMADV (“duh-mad-vee”, /də.ˈmæd.vi/) is used for projects aimed at creating new product or process designs
DMAIC
DMAIC’s five steps
The DMAIC project methodology has five phases:
- Define the system, the voice of the customer and their requirements, and the project goals, specifically.
- Measure key aspects of the current process and collect relevant data; calculate the “as-is” process capability
- Analyze the data to investigate and verify cause and effect. Determine what the relationships are, and attempt to ensure that all factors have been considered. Seek out the root cause of the defect under investigation.
- Improve or optimize the current process based upon data analysis using techniques such as design of experiments, poka yoke or mistake proofing, and standard work to create a new, future state process. Set up pilot runs to establish process capability.
- Control the future state process to ensure that any deviations from the target are corrected before they result in defects. Implement control systems such as statistical process control, production boards, visual workplaces, and continuously monitor the process. This process is repeated until the desired quality level is obtained.
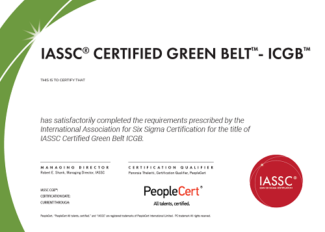
Some organizations add a Recognize step at the beginning, which is to recognize the right problem to work on, thus yielding an RDMAIC methodology.
DMADV
DMADV’s five steps
Also known as DFSS (“Design For Six Sigma”), the DMADV methodology’s five phases are:
- Define design goals that are consistent with customer demands and the enterprise strategy.
- Measure and identify CTQs (characteristics that are Critical To Quality), measure product capabilities, production process capability, and measure risks.
- Analyze to develop and design alternatives
- Design an improved alternative, best suited per analysis in the previous step
- Verify the design, set up pilot runs, implement the production process and hand it over to the process owner(s).
Professionalization
One key innovation of Six Sigma involves professionalizing quality management. Prior to Six Sigma, quality management was largely relegated to the production floor and to statisticians in a separate quality department. Formal Six Sigma programs adopt an elite ranking terminology similar to martial arts systems like judo to define a hierarchy (and career path) that spans business functions and levels.
Six Sigma identifies several roles for successful implementation:
- Executive Leadership includes the CEO and other members of top management. They are responsible for setting up a vision for Six Sigma implementation. They also empower other stakeholders with the freedom and resources to transcend departmental barriers and overcome resistance to change.
- Champions take responsibility for Six Sigma implementation across the organization. The Executive Leadership draws them from upper management. Champions also act as mentors to Black Belts.
- Master Black Belts, identified by Champions, act as in-house coaches on Six Sigma. They devote all of their time to Six Sigma, assisting Champions and guiding Black Belts and Green Belts. In addition to statistical tasks, they ensure that Six Sigma is applied consistently across departments and job functions.
- Black Belts operate under Master Black Belts to apply Six Sigma to specific projects. They also devote all of their time to Six Sigma. They primarily focus on Six Sigma project execution and special leadership with special tasks, whereas Champions and Master Black Belts focus on identifying projects/functions for Six Sigma.
- Green Belts are the employees who take up Six Sigma implementation along with their other job responsibilities, operating under the guidance of Black Belts.
According to proponents, special training is needed for all of these practitioners to ensure that they follow the methodology and use the data-driven approach correctly.
Some organizations use additional belt colors, such as “yellow belts”, for employees that have basic training in Six Sigma tools and generally participate in projects, and “white belts” for those locally trained in the concepts but do not participate in the project team. “Orange belts” are also mentioned to be used for special cases.
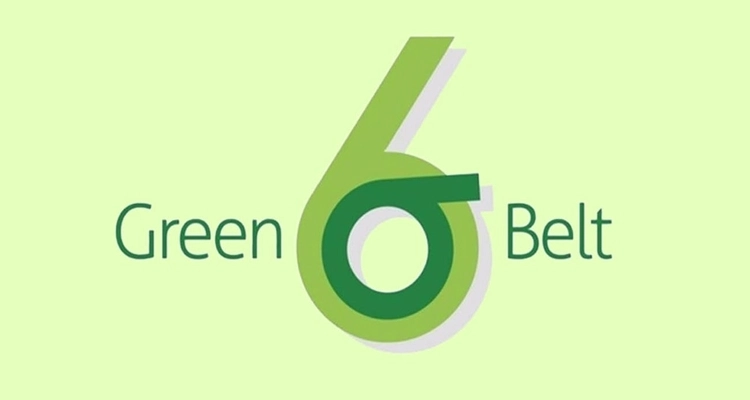
General Electric and Motorola developed certification programs as part of their Six Sigma implementation. Following this approach, many organizations in the 1990s started offering Six Sigma certifications to their employees. In 2008 Motorola University later co-developed with Vative and the Lean Six Sigma Society of Professionals a set of comparable certification standards for Lean Certification. Criteria for Green Belt and Black Belt certification vary; some companies simply require participation in a course and a Six Sigma project. There is no standard certification body, and different certifications are offered by various quality associations for a fee. The American Society for Quality, for example, requires Black Belt applicants to pass a written exam and to provide a signed affidavit stating that they have completed two projects or one project combined with three years’ practical experience in the body of knowledge.