Courtesy: ISO 10015 quality management guidelines for training
Software
Quality management software offers the techniques, processes, structure, and resources needed to simplify manufacturing and ERP activities while handling quality concerns efficiently and cost-effectively.
Helps manufacturers to monitor, control, and document quality processes electronically to guarantee that goods are made within tolerance, meet all necessary requirements, and are defect-free. Quality management software is often used in the manufacturing industry to identify potential issues before they occur.
Some benefits of quality management software include:
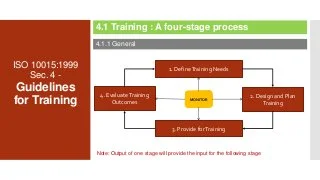
- real-time data monitoring
- issue prevention
- risk management
- increased efficiency and productivity
- process consistency
- increased employee participation
Quality management software can be integrated with manufacturing execution systems (MES). A MES is a complete, dynamic software system for monitoring, tracking, documenting, and controlling the manufacturing process from raw materials to final products. When combined with QMS, these systems:
- ensure compliance
- enable quality programs
- eliminate waste
- less product recalls
- lower per-product cost
- higher product quality
- real-time information for increase in quality control
- realistic production schedules
- up-to-date inventory
- product tracking
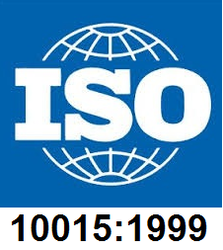
Quality management software focuses on 4 main elements:
- Document management: Quality management software enables companies to manage all product and quality records and documents, including product specifications, work instructions, standard operating procedures (SOPs), quality policies, and training records, among other things, to fulfill highly regulated requirements. Quality management software centralizes the storage of these documents.
- Regulatory compliance: To decrease compliance risks, quality management software is used within companies to make sure they comply with ISO, OSHA, FDA, and other industry norms and requirements. The software makes closed-loop corrective and preventive action procedures (CAPA) possible, which result in faster issue resolution and issue prevention.
- Feedback loops: Quality management software permits staff to submit feedback or recommendations through centralized software. In turn, this way, managers gather insights from the shop floor creating a feedback loop.
- Training and skill management: To maintain product quality, quality management software can provide a fixed system through which employees and staff can be trained. This fixed system provides more clarity in the different tracking processes of the company and simplifies the tracking of different skill levels of employees.
Most quality management software are cloud-based and offer software as a service.